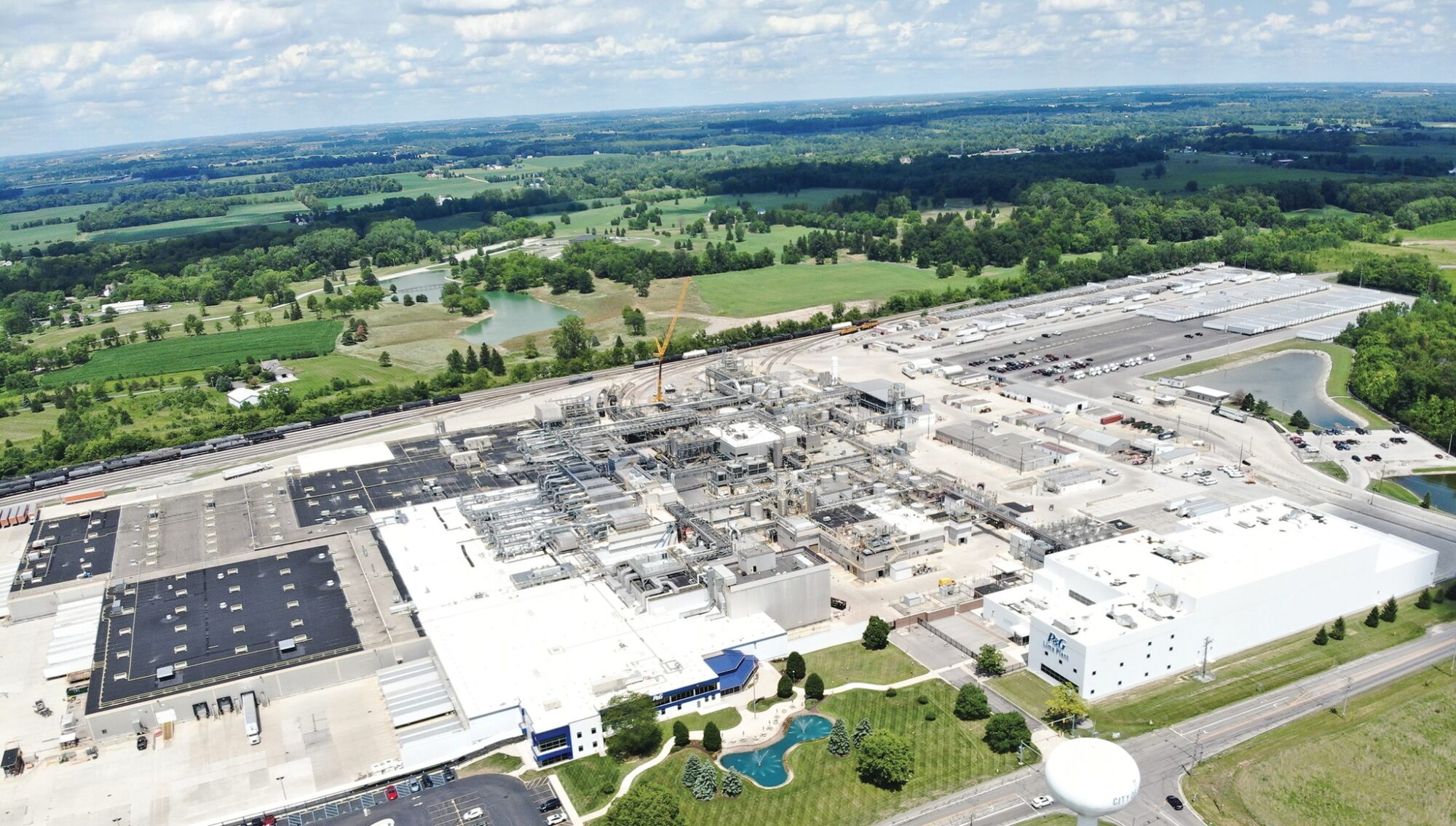
Jul 26 Top Three Factors to Consider When Renovating a Manufacturing Facility
Renovating a manufacturing facility can be a complex and challenging process. Here are three top factors to keep in mind to ensure a successful renovation:
- Comprehensive Planning and Analysis: Before starting any project—especially a renovation project—it’s fundamental to conduct comprehensive planning and analysis. This involves assessing the current state of the facility, identifying areas that require improvement, and setting clear goals for the renovation. “Experience has taught us that communication is the most important part of renovating a manufacturing facility,” said Clinton Kurtz, H. J. Russell & Company’s division manager for industrial mission critical projects. “By creating a clear vision with the plant operators along with the construction team we can be successful.” Engage with major stakeholders, including employees, engineers and management, to gather valuable insights and feedback. Consider factors like workflow optimization, equipment upgrades, safety enhancements, energy efficiency, and compliance with industry regulations. A well-thought-out plan will help you avoid costly hiccups and ensure that the renovation aligns with the long-term needs and objectives of the facility.
- Minimize Downtime and Disruptions: Because manufacturing facilities often run 24/7, any renovation can lead to disruptions in production and operations. So, minimizing downtime is critical to avoid substantial financial losses. Develop a detailed timeline and schedule the renovation in phases, if possible, to keep production running smoothly. Prioritize critical areas that need renovation, and consider carrying out less disruptive work during off-peak hours. Additionally, communicate with the workforce throughout the process to manage expectations and provide them with alternative work arrangements, if necessary.
- Safety First: Safety should always be take precedence during any renovation project, especially in manufacturing facilities with potential hazards. Conduct a thorough risk assessment and take necessary precautions to protect employees as well as equipment. Ensure that everyone involved in the renovation, including contractors and subcontractors, adheres to safety protocols and standards. Provide appropriate training and safety equipment, and encourage open communication about safety concerns. A safe and secure work environment will lead to a more efficient renovation and, most importantly, safeguard the well-being of all those involved.
Remember that renovating a manufacturing facility is a significant undertaking that requires careful planning, execution, and ongoing monitoring. By considering these top factors, you can enhance the likelihood of a successful renovation that meets the facility’s needs and improves its overall productivity and efficiency.